
Process Consultants Inc.
Project Management -- Engineering -- Design -- Food Processing Solutions
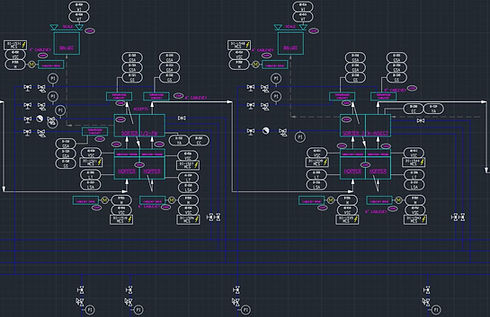
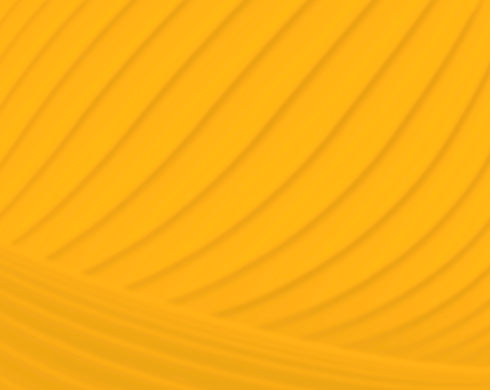
About Us
Established in 2015, Process Consultants Inc. offers high quality engineering design and project management services, specializing in the manufacturing and food processing industries.
Located in California’s Central Valley, we are ideally positioned to service the industries located in one of the most productive agricultural regions in the world, providing more than half of the fruits, vegetables, and nuts grown in the United States.
​
Process Consultants works closely with operational leadership to provide the best possible product(s), output(s), and efficiency to help reach the desired financial goal(s). We strive to achieve the best quality manufacturing and process designs, holding the following in focus:
​
-
Personnel Safety
-
Food Safety
-
Minimizing Yield Losses
-
Balancing automation for product consistency
-
Minimizing labor costs
-
Avoiding excessive complexity
-
Maintain operational efficiency
-
Meeting budgetary needs
-
Helping find acceptable installation costs
-
Providing low operational costs for the long term
Services Performed
Process Consultants is hired directly by food and beverage companies as well as sub-contracted by large engineering and construction firms to plan, develop, and coordinate food processing solutions. Our projects are broken down into phases, which typically can include all or some of the following:
​
CONCEPTUAL DESIGN
-
Determining General Requirements of Project
-
Creating & Reviewing Innovative Line Designs & Layout Options
-
Obtaining Crucial Vendor Lead Times & Cost Estimates
-
Defining Preliminary Project Rationale, Budget & Time-frame
​
FINAL DESIGN
-
Concluding Line Design, Layouts & Equipment Specifications
-
Ascertaining System Controls, Utilities & Documentation Requirements
-
Refining Project Scope, Schedule & Cost
-
Allocating Funds & Resources to Meet Project Objectives
-
Authorizing Project Plan & Execution with Client
IMPLEMENTATION
-
Ordering Equipment & Verifying Machinery Designs
-
Preparing & Distributing Contractor Bid Packages for Appropriate Selections
-
Fully Developing Project Schedule & Critical Path
-
Performing Critical Equipment Pre-Shipment Acceptance Tests
-
Coordinating Site-Preparation & Equipment Installation Activities
-
Managing Contractor & Vendor Activities On-Site
-
Arranging Operator & Maintenance Training Sessions
START-UP THROUGH COMMISSIONING
-
Coordinating Support Activities for Equipment Start-Up & Line Debug
-
Arranging Production Line Ramp-Up with Client
-
Testing Equipment Performance in Production to Approve Final Payments
-
Performing Technical & Financial Project Follow-Up

Clientele

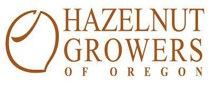






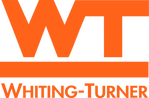
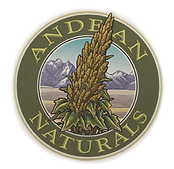_edited.png)
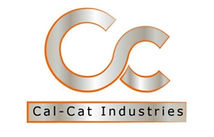
